Machine Integration
180 Systems has assisted clients in machine integrations with a proven project structure and methodology
Just bought a new machine and need to integrate it with your systems?
- Machines can be unique
- Software vendors may or may not have integrated to your type of machine before
- Critical mistakes need to be avoided to get your machine up and running correctly
- Mistakes are not acceptable
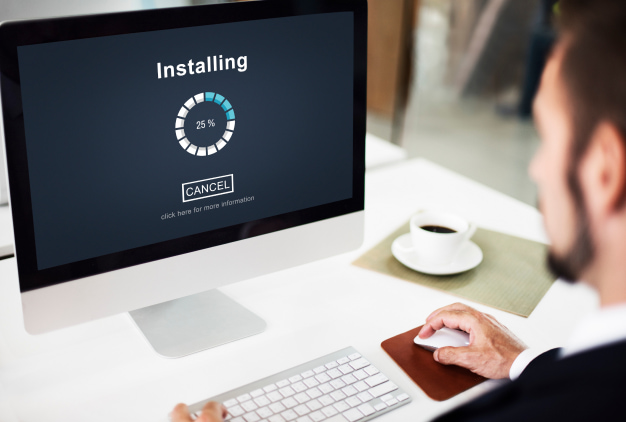
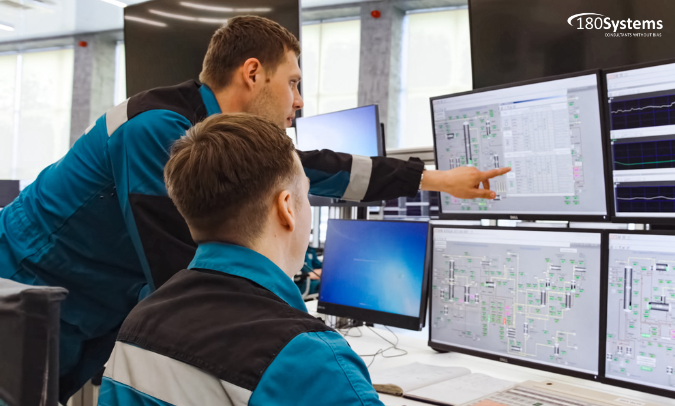
Our independent technology consultants will
- Ensure your machine is integrated to your systems for success
- Ensure all sections are covered for a smooth machine GoLive
- Prepare a testing script tincluding health & safety
- Upgrade GoLive readiness assessment and checklists
180 Methodology
Stage 1: Project Initiation
Covers initial plan creation, alignment with client and vendors, organizational structuring, governance setup, kickoff, scheduling regular progress reviews, and sign-off procedures
Stage 2: Systems Integration & Development Work
Detail and validate system integration needs/scope, confirm security endpoints and access, complete required development work
Stage 3: 1st Build & Prep for Machine Arrival
Machine built at vendor facility (if required), vendor machine testing & initial sign-off, dis-assembly/prep for shipping, client prep for machine arrival including required machinery and tools, shipment to client site
Stage 4: Machine Build at Client Site
Mechanical and electrical assembly, PLC configuration, network setup unloading, hardware installation, culminating in the completion of the machine build at the client site.
Stage 5: Training, Testing, and Cutover
All machine operators and office staff are trained on , conducting comprehensive staff training, preparing and assessing test cases, and concluding with User Acceptance Testing sign-off.
Stage 6: Go-Live
Start running orders in your new system